A torque wrench is a specialized tool designed to apply a specific amount of force to a fastener, such as a nut or bolt. This tool is essential in many industries, including automotive, construction, and especially aviation. The torque wrench or torque screwdriver measures the amount of turning or twisting force applied to a nut, bolt, or screw.
Aircraft are made of thousands of parts held together by numerous bolts or fasteners, each of which must be tightened with a very precise amount of torque to withstand varying degrees of altitude, speed, and temperature. Therefore, torque wrenches play a vital role in ensuring the safety, reliability, and longevity of aircraft.
Importance of Torquing
As aircraft speed increases, each structural member becomes more stressed. It is therefore extremely important that each member carry neither more nor less load than it is designed for. To distribute the loads safely throughout a structure, proper torque must be applied to all nuts, bolts, studs, and screws.
Proper torque of fasteners used in aviation is critical to continued safe operation.
Using the proper torque allows the structure to develop its designed strength and greatly reduces the possibility of failure due to fatigue.
Types of Torque Wrenches
The three most commonly used torque wrenches in aviation are the flexible beam, rigid frame, and ratchet types. When using a flexible beam or rigid frame torque wrench, the torque value is read visually on a dial or scale mounted on the handle.
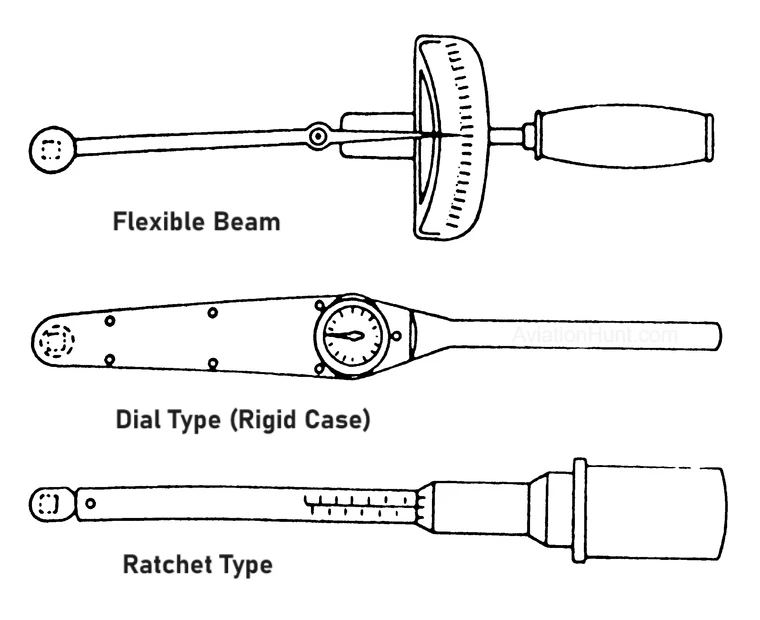
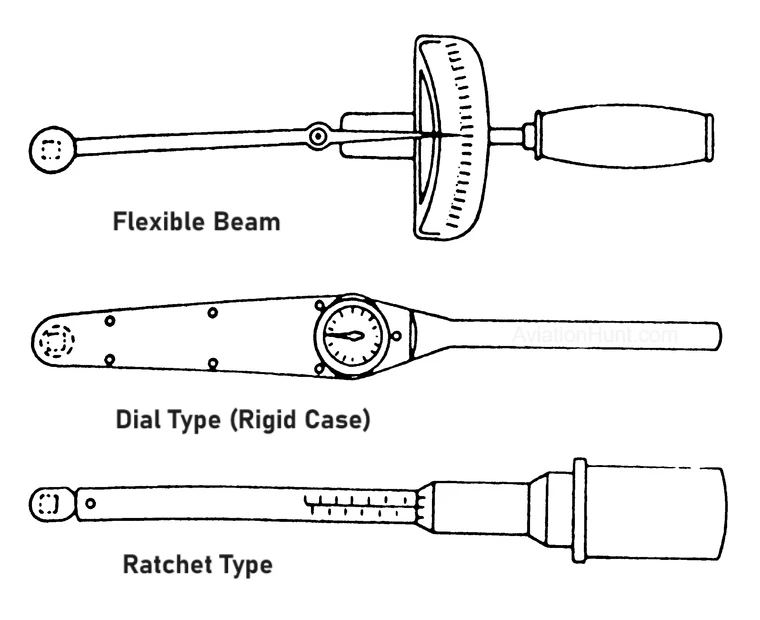
Flexible Beam Torque Wrench
A flexible beam torque wrench is easy to operate. When torque is applied to the handle, the needle moves to the right or left indicating the amount of torque applied. Once the torque pressure is removed, the needle automatically returns to zero. Its pivoted handle concentrates the applied turning force at the precise point on the lever to assure torque accuracy. This torque wrench can be used in both left and right-hand directions. Accuracy is +/- 2%.
How to use a Flexible Beam torque wrench:
- Install the proper size socket onto the drive end of the torque wrench.
- Put the socket onto the but to be tightened. If necessary, hold the head of the bolt with the appropriate size wrench.
- Pull the wrench with a smooth and steady motion. Keep the direction of the pull at right angles to the handle.
- Be sure to apply the force to the center of the handle. If the handle has a pivot point, apply the force to keep the handle centered on the pivot point.
- Tighten the nut (or bolt) until the reading on the scale matches the required torque.
Note: If the pointer does not point to zero when no torque is being applied, the torque wrench is out of calibration and must not be used.
Dial Type Torque Wrench
It is named for its easy-to-read torque measurement dial. It allows the operator to quickly identify the torque being applied. It measures torque by way of a needle that moves inside the dial. It can be used in both directions.
How to use a Dial Type torque wrench:
- Install the proper size socket onto the drive end of the torque wrench.
- Put the socket onto the but to be tightened. If necessary, hold the head of the bolt with the appropriate size wrench.
- Pull the wrench with a smooth and steady motion. Keep the direction of the pull at right angles to the handle.
- Torque the nut (or bolt) until the reading on the dial matches the intended torque value.
Note: If the dial does not read zero when no torque is being applied adjust the dial to read zero. If the dial is not adjustable the wrench is out of calibration and must not be used.
Ratchet Type Torque Wrench
With this torque wrench, the desired torque is determined before the wrench is used by turning the micrometer-like thimble above the handle to the desired setting on the shaft of the torque wrench. Once the set torque value is reached a click can be felt and heard. Most are designed for use in only one direction (either clockwise or counter-clockwise).
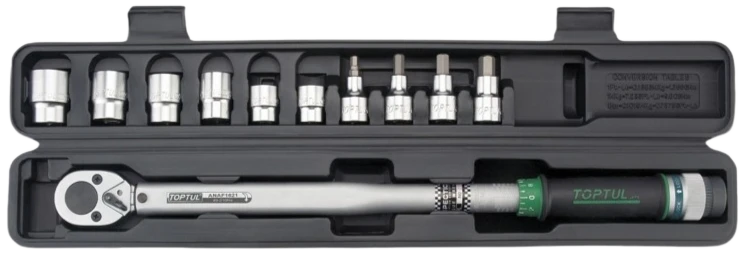
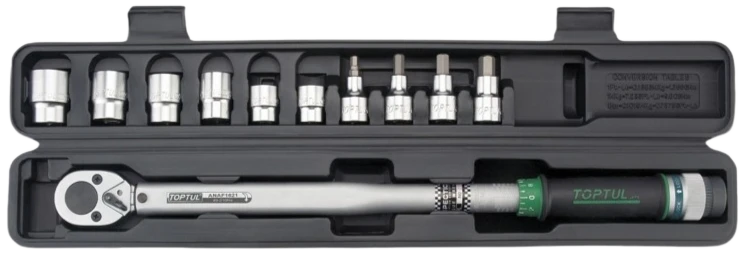
How to use a Ratchet Type torque wrench:
- Unlock the grip and adjust the handle to the desired setting on the micrometer-type scale, then relock the grip.
- Install the required socket or adapter to the square drive of the handle.
- Place the wrench assembly on the nut or bolt, and pull the wrench assembly on the nut or bolt in a clockwise direction with a smooth, steady motion.
- A fast or jerky motion results in an improperly torqued unit.
- When the applied torque reaches the torque value indicated on the handle setting, the handle automatically releases or “breaks” and moves freely for a short distance.
- The release and free travel is easily felt, so there is no doubt about when the torqueing process is completed.
How to use a Torque Wrench
Always follow the maintenance manual’s procedures for torque wrench use. When the torque value for a particular fastener or fitting is not specified in the aircraft or engine’s maintenance manual procedures, the mechanic should use the torque values listed in the maintenance manual’s standard torque tables.
Check Calibration
Before you use a torque wrench, make sure the calibration is correct. A calibration certificate is provided by the calibration laboratory or facility for the specific torque wrench that they have calibrated. This certificate contains important details such as the date of calibration, the values at which the calibration was performed, and the amount of error observed during the calibration process.
An uncalibrated torque wrench may not provide the correct torque, leading to over-tightening or under-tightening. Over-tightening can damage the threads of a stud or lug nut, while under-tightening can loosen a bolt, both of which can lead to accidents.
Do not use the torque wrench if the calibration sticker is missing or expired.
Range to Use
Make sure the capacity of the wrench you select is rated above the torque required. Never exceed or go below the torque value range of the torque wrench.
It is recommended to use a torque wrench with a value between 30% and 80% of its range for a given torque value. For example – a torque wrench of maximum 10 m.daN:
- Torque wrench range from 2 m.daN to 10 m.daN,
- Recommended range 3 m.daN to 8 m.daN.
Only moderate force is required to obtain the correct torque in the recommended range. You can feel an increase in force when you apply torque.
How to Hold
The torque wrench axes must be perpendicular to the fastener axis. Put your hand on the handle and pull it along the axis. Apply the torque value gradually and perpendicularly to the wrench. Stop the movement when the wrench releases (or on the signal).
Use Correctly
Make sure that the torque is applied correctly. You can apply unwanted torsion or flexion to the component if the position of the wrench (or the screwdriver) is incorrect. Applying the tightening torque incorrectly can change the tightening torque and thus the preload.
Caution: Do not use the torque wrench as a breaker bar or to loosen nuts or bolts.
Use of Adapter
Sometimes you may need to torque fasteners that are difficult to get to locations. When this happens
you might need to use an extension attached to the torque wrench to apply the torque.
There are two types of extensions. They are the handle extensions and drive end extensions (adapter).
Do not use a handle extension with the flexible beam-type torque wrench as this will cause inaccurate torque readings. Handle extensions may be used on the rigid frame and snap-type torque wrenches as extensions on these types of torque wrenches do not change the torque applied to the fastener.
Using an extension on the drive end (except when that extension (adapter) is at 90 degrees to the torque wrench frame) will change the required torque reading on the torque wrench. If the maintenance manual instructs you to use an extension, it will give you the required changes / corrections to the torque wrench readings. If the maintenance manual does not tell you to use an extension, or you decide to use an extension on your own, use the following formula to calculate the corrected torque value to be indicated on the torque wrench for the required torque needed on the fastener. Failure to make these corrections will result in the wrong torques being applied and may result in serious installation errors.
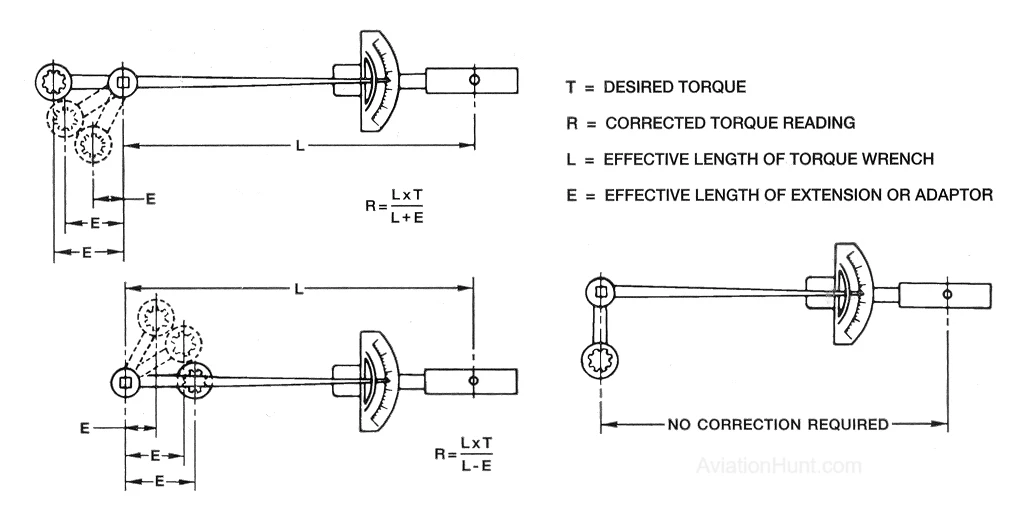
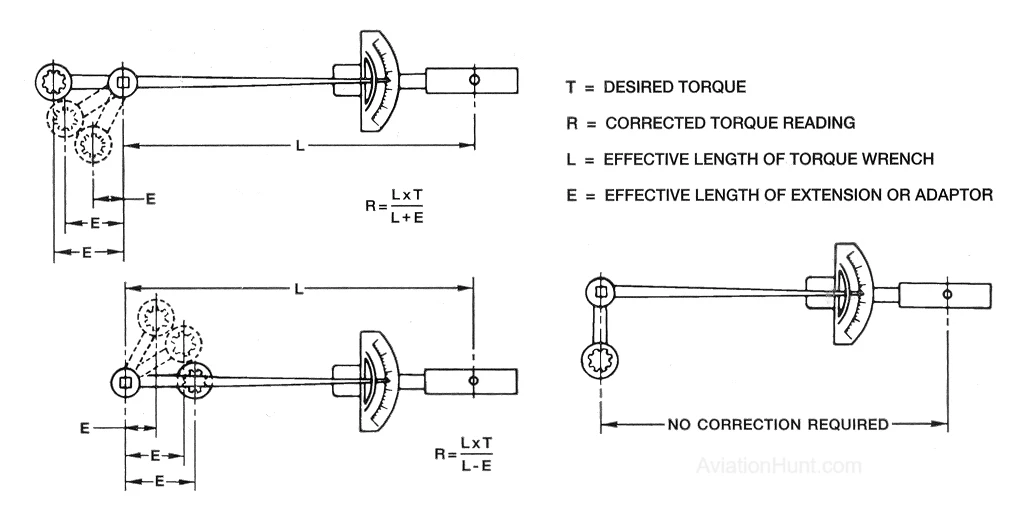
When you use an adapter the value shown on the dial of the torque wrench is not the applied value. Make sure that the length of the torque wrench is more than the length of the adapter.
Torque-value correction is applicable when the adapter is used. To pre-calibrate the torque wrench, you can use this formula to get the torque wrench dial reading:
R = (T x L) / (L + E)
- T: Value that you must apply on the fastener
- L: Length of the torque wrench
- E: Length of the adapter
- R: Torque-wrench dial-reading
Calibrate the torque wrench and the adapter assembly on the torque meter.
- Adjust the R value until you get the T value on the torque meter.
- Do the tightening operations five times, one after the other to make sure that the torque wrench and the adapter are calibrated correctly.
After Use
To maintain the accuracy of a mechanical click-type torque wrench, it is recommended to dial it down to its lowest value after use. This helps to relieve the tension on the spring mechanism, which triggers the click at the correct torque.
General Tips
- To obtain values in foot-pounds, divide inch-pounds by 12.
- Always tighten by rotating the nut first if possible. When space considerations make it necessary to tighten by rotating the bolt head, approach the high side of the indicated torque range. Do not exceed the maximum allowable torque value.
- Maximum torque ranges should be used only when materials and surfaces being joined are of sufficient thickness, area, and strength to resist breaking, warping, or other damage.
- When torturing a nut-bolt combination, always hold the end, opposite to the one being torqued, with a wrench. This is done to keep the entire assembly from rotating as torque is being applied.
- Always use a backup wrench when tightening couplings and bulkhead style fittings. Back the fitting and tighten the nut in all cases.
- For accurate torquing, the final turn of the nut or bolt must be made with the torque wrench.
- Re-check torque on the fastener.
Torquing Sequence
When there are several bolts to tighten on a component (especially when they are in a circular arrangement) they must be tightened in a specific sequence that is normally specified in the manual. If it is not specified, torque the bolts 180 degrees apart.
This technique reduces the strain on the fasteners and allows the parts to be seated correctly and for the loads to be equally distributed.
The torquing, installation, or tightening sequence is given in the procedure. If it is not given in the procedure, you can use the standard sequence.
For the standard torquing sequence to assemble the fasteners, see the following diagram.
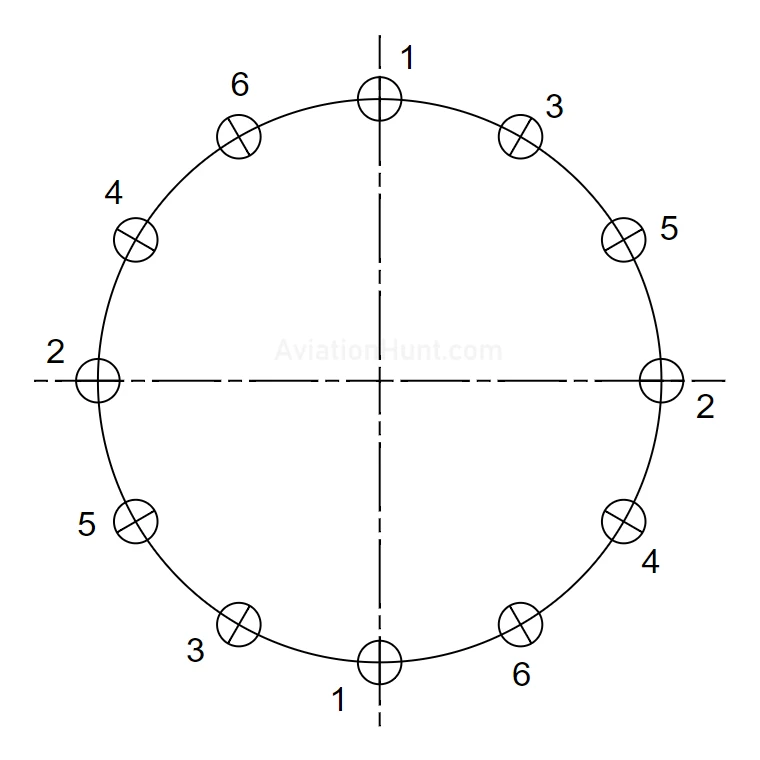
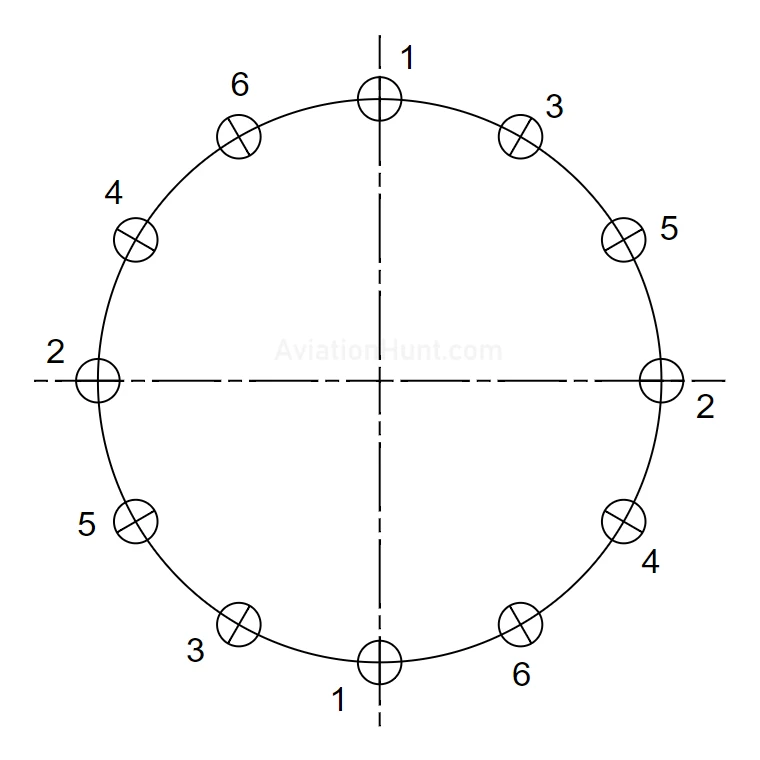
Definition of various Torques
Here are the definitions of various torques used in aviation to tighten fasteners.
Applied Torque
The applied torque is the torque which the installation tool transmits to the fasteners.
Tightening Torque
The assembly, installation, or tightening torque is the design torque applied at the final assembly.
This torque is a combination of these torques –
- The torque necessary to overcome the kinetic friction between the mating surfaces of the bearing faces and threads.
- The torque necessary to overcome the self-locking feature (if there is one).
- The torque necessary to apply the correct axial load to a fastener assembly.
The word “MAXIMUM” or “MINIMUM” can be specified before the torque value and refers to the upper or lower tolerance of the nominal torque value. The assembly, installation, or tightening torque is measured only in the tightening direction.
Breakaway Torque
The breakaway torque applies only to fasteners that have self-locking mechanisms. The breakaway torque is the torque necessary to start the relative movement between male and female threads, when:
- The self-locking mechanism is fully engaged.
- There is no contact between the bearing surface of the fastener and the material attached by this fastener.
The word “MAXIMUM” or “MINIMUM” can be specified before the torque value and refers to the upper or lower tolerance of the nominal torque value. The breakaway torque is measured only in the loosening direction.
Double Torque
The double torque or re-torque is the torque necessary to fully seat the materials that are attached when there are moderate interferences, sheet gaps or form-in-place gaskets.
For a double torque or re-torque, it is necessary to obey this sequence:
- Apply the installation torque.
- Loosen the fasteners.
- Apply the installation torque again to make sure that the fasteners are attached correctly.
Free Running Torque
The free running torque is the torque necessary to overcome the kinetic friction between the mating threads. This torque is measured in the loosening or tightening direction.
This type of torque does not overcome:
- Self-locking mechanisms.
- Axial loads in fastener assemblies.
This type of torque is not applicable for fasteners that have self-locking mechanisms.
Multiple Torque
The multiple torque is the torque necessary to seat the parts to be assembled where there is a heavy interference in the assembly. Multiple torquing is the application of the installation torque again and again until the fastener does not turn during two installation-torque applications, one after the other.
Net Torque
The net torque or preload torque is the component of the installation torque used for the axial loading of a fastener assembly after you overcome all the frictional and mechanical forces (but not the axial tension).
Net torque = Installation torque – Torque necessary to overcome the frictional torque (prevailing torque) and mechanical torque.
Over Torque
The over-torque or over-tightening torque is the torque necessary to move a torqued fastener from the installed condition. This torque is always measured in the tightening direction and is usually more than the maximum limit of the installation torque.
It is usually used to:
- Overcome or loosen the heat seizure effects before corrosion occurs when the fastener assembly is disassembled.
- Deform the captive internal-thread elements in blind fasteners with threaded cores.
Prevailing Torque
The prevailing, run down or self-locking torque is the torque necessary, when a fastener is not seated correctly, to overcome:
- The kinetic friction of the mating threads, and
- The locking feature when the locking feature is fully engaged.
The prevailing torque does not include axial-load torque effects. The prevailing torque is measured in the loosening or tightening direction while the fastener is in movement.
Seating Torque
The seating torque is the torque necessary to put the bearing faces in the seated position. The seating torque is measured only in the tightening direction.
Single Torque
The single torque is the installation torque applied one time to each assembly, usually to the freely fitting parts, where there are no interference fits to prevent the seating of the mating parts.
Torque Tension
This term torque tension refers to the residual axial stress in a fastener caused by the applied net torque. It is also used to give the relationship between the net torque and preload in the threaded fasteners.